目录
precision turning processing is a machining method by rotating the workpiece and using the tool to cut. It is widely used in the manufacturing industry for its high precision, high efficiency, and automation.
The process flow of precision turning
Before turning, we must first prepare the process. It mainly includes the following aspects:
First, we determine the blank allowance, drawings, and technical requirements of the machined parts, and understand the size, shape, material, and other information of the parts. then we select the right tool, measuring tool, and fixture to ensure the turning performance and durability of the tool. At last time, we determine the machining sequence and turning route to reduce the machining time and improve machining quality.
Clamping workpiece: The workpiece to be machined is clamped on the lathe, we ensure that the workpiece axis coincides with the spindle axis of the lathe, and the clamping force is appropriate. We must pay attention to the balance of the workpiece to prevent vibration during processing when clamping.
Adjust the tool: We accord to the size and material of the machined parts, and adjust the tuning parameters of the tool, such as the extension length of the tool, the angle of the tooltip, the tool speed, etc. At the same time, it is necessary to ensure the sharpness of the tool to improve the processing quality.
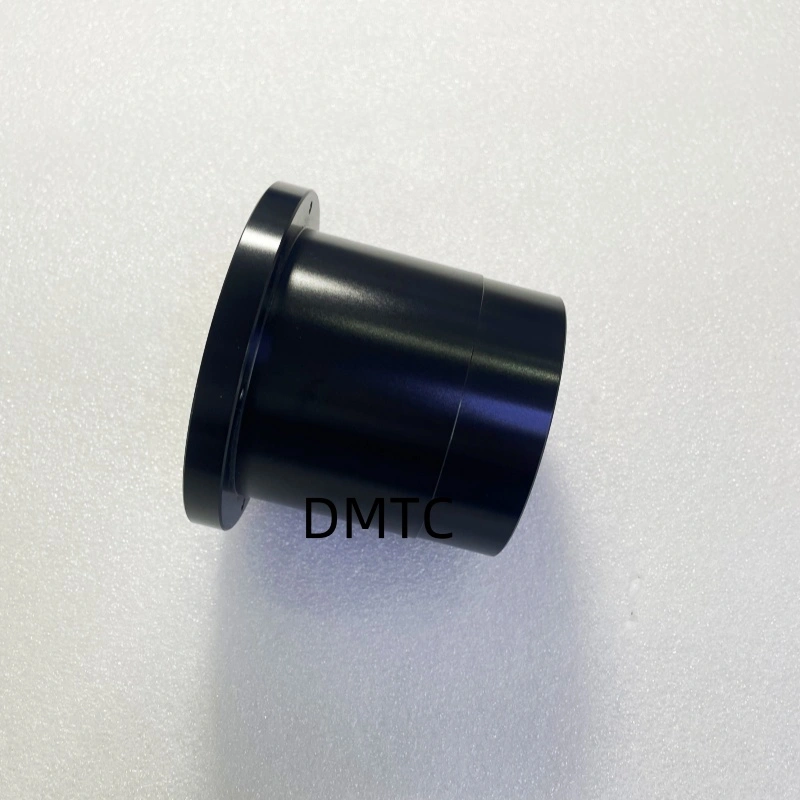
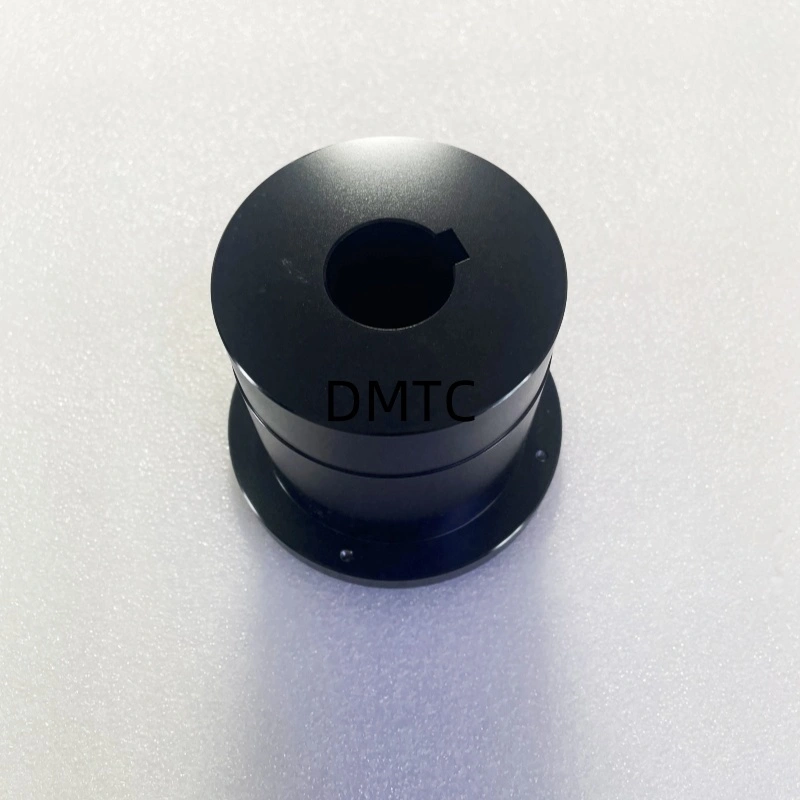
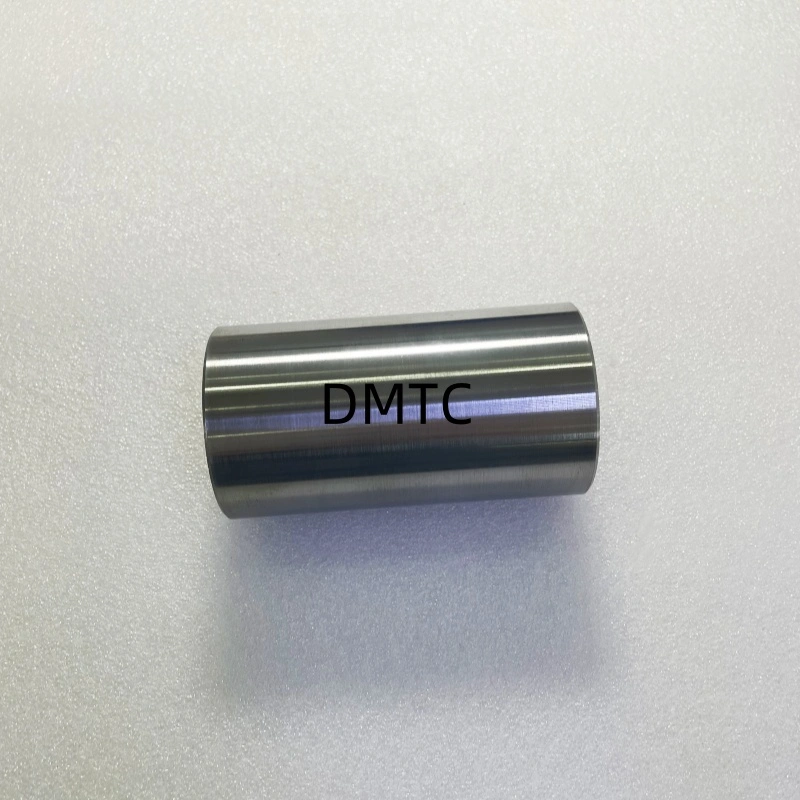
Turning processing mainly includes the following stages:
Rough turning: The use of larger turning depth and faster tool speed for preliminary processing to quickly remove the rough surface of the workpiece.
Semi-finishing: reduce the turning depth, improve the tool speed, and make the workpiece surface reach the predetermined size and finish.
Fine-tuning: further reduces the turning depth, reduces the tool speed, and improves the dimensional accuracy and flatness of the workpiece.
Polishing: Using a smaller turning depth and slower tool speed to further improve the finish of the workpiece surface.
Inspection and dressing: After the turning process is completed, the workpiece needs to be inspected to ensure that the processing quality reaches the technical requirements. Inspection contents include size, shape, surface finish, etc. If excessive defects are found, they need to be repaired.
Parts removal: Machining qualified parts are removed from the lathe for subsequent processing or finished product acceptance.
The differences between precision turning and traditional turning
1:processing technology is different
In the traditional turning process, positioning benchmarks, clamping methods, tools, etc., can be simplified, but the data processing process is more complex, precision turning has a variety of solutions, it can process a variety of processing parts, and the process is diversified.
2:Different clamping fixtures
In the process of precision turning, not only the coordinate direction of the fixture and the machine tool is relatively fixed, but also the dimension relationship between the parts and the machine coordinate system should be coordinated. In the process of clamping, it is necessary to effectively control the positioning and clamping. In the traditional turning process, the capacity of the machine is limited, it is necessary to carry out multiple clamping in the processing process. The need to use special fixtures, results in higher fixture design and manufacturing costs, so it increases the production cost of the product. The position of the precision turning process can be adjusted by the instrument. This reduces unnecessary production costs.
3:Different knives
In the processing, the choice of tools needs to be determined according to the processing technology and processing method. Especially in precision turning processing, the use of high-speed turning is not only conducive to improving the processing efficiency, but also to ensuring the quality of processing, it effectively reduces the probability of turning deformation, and shortens the processing cycle, compared with traditional turning processing, precision turning processing has higher performance requirements for the tool.
The application of precision turning processing
Turning is a common metal-cutting process, that is widely used in the field of machinery manufacturing. It is mainly used for processing rotationally symmetrical metal parts, such as shafts, gears, threads, etc. The turning process is complicated, but if we adopt reasonable design and operation, the fine production of metal parts can be realized.
With the progress of science and technology and the development of Industry 4.0, turning processing will meet more development opportunities. The popularization of digital manufacturing technology will make the turning process more intelligent and efficient. At the same time, the application of new materials and processes will bring more challenges and opportunities for turning processing. In a word, turning is a processing method that is full of skills and art, and it plays an important role in the modern manufacturing industry.
DMTC owns sophisticated equipment and professional technicians. We can machine a variety of parts, can professionally customize a variety of products that you need, every product before delivery has been strictly tested and inspected to ensure the quality of the product. If you need professional customized turning services, DMTC will be a good choice.
0