目录
Proper installation of safety valves is crucial for ensuring their effective operation and maintaining the safety of the system. Here are the key precautions and setting points to consider:
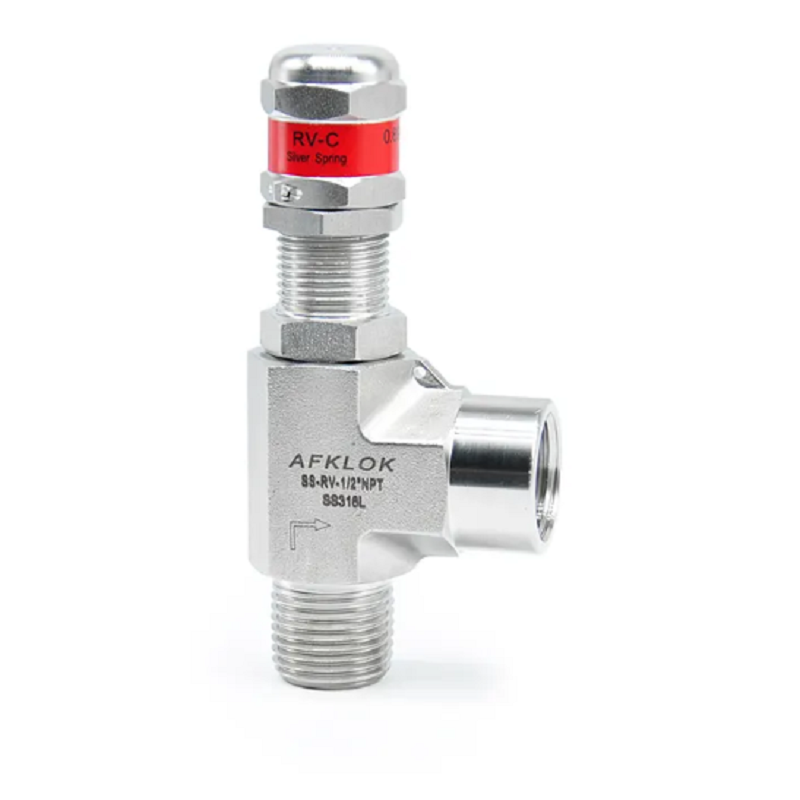
Setting Points
1. Gas and Liquid Materials:
– Installation Location: When the container contains both gas and liquid materials, the safety valve should be installed in the gas phase.
– Rationale: This ensures that the safety valve can effectively relieve overpressure without being affected by liquid presence.
2. Flammable Liquid Discharge:
– Accident Storage Tank: Connect the outlet of the safety valve to an accident storage tank if it discharges flammable liquids.
-Protective Facilities: If the discharged material is high-temperature combustible, the receiving container should have appropriate protective facilities to prevent fires or explosions.
3. Venting On-Site:
– Height Requirement: The vent should be at least 1 meter higher than the operator and should not be directed towards open flames, spark sites, or high-temperature equipment within 15 meters.
– Indoor Equipment: For indoor equipment, the vent should extend above the roof and be at least 2 meters higher than the roof.
– Rationale: This ensures that the discharged material does not pose a hazard to personnel or nearby equipment.
4. Block Valve at Inlet:
– State: If a block valve is installed at the inlet of the safety valve, it should be in a normally open state and sealed with lead to prevent accidental closure.
– Rationale: This ensures that the safety valve can operate freely when needed.
Import and Export Pipeline
1. Cross-Sectional Area:
– Inlet Cross-Section: The cross-sectional area of the connecting pipes and fittings between the safety valve and the boiler or pressure vessel should not be less than the cross-sectional area of the inlet of the safety valve.
– Shared Inlet Pipeline: If several safety valves share an inlet pipeline, the cross-sectional area of the inlet pipeline should not be less than the sum of the cross-sectional areas of the safety valves.
– Rationale: This ensures that the flow is not restricted and the safety valve can operate effectively.
2. Cut-Off Valves:
– General Rule: Generally, no cut-off valves or steam outlet pipes should be installed between the safety valve and the drum or header of the boiler, or between the safety valve and the pressure vessel.
– Exceptions: For pressure vessels containing flammable, corrosive, viscous media, or valuable media with high toxicity, a stop valve can be installed with the approval of the technical director and with reliable preventive measures in place.
– Operation: During normal operation, the cut-off valve must be fully opened, sealed, or locked.
– Rationale: This prevents interference with the safe discharge of the safety valve.
3. Threaded Connection:
-Short Pipe: Spring-type safety valves with threaded connections should be connected to a short pipe with threads, which should be welded to the cylinder or header.
– Rationale: This ensures a secure and leak-free connection.
4. Discharge Pipe:
– Avoid Twists and Turns: The discharge pipe should be as straight as possible to minimize resistance.
– Exhaust Location: The exhaust pipe should lead to a safe place with sufficient cross-sectional area to ensure smooth exhaust.
– Chemical Reactions: Safety valves that can interact to produce chemical reactions should not share a discharge pipe.
– Corrosive and Combustible Gases: For equipment with corrosive and combustible gases, take measures to prevent corrosion or fire and explosion during discharge.
– Toxic Medium: If the medium is toxic and has a vapor density greater than air, the discharged medium should be introduced into a closed system for recovery and reuse.
– Rationale: These measures ensure the safe and controlled discharge of the medium.
5. Fixed Discharge Pipe:
– Support: The discharge pipe of the safety valve should be fixed to prevent excessive additional stress or vibration.
– Rationale: This ensures the structural integrity and stable operation of the safety valve.
6. Freezing Prevention:
-Outdoor Valves: Safety valves installed outdoors should have reliable measures to prevent the water in the medium from freezing when the temperature drops below 0°C.
– Rationale: This prevents blockages and ensures the valve can operate when needed.
7. Crystallization Prevention:
– Heat Insulation: If the crystallization temperature of the medium is higher than the minimum ambient temperature, the safety valve must be equipped with a heat preservation jacket and installed with heat preservation purging steam.
– Piping Design: The inlet and outlet pipelines of the safety valve should be designed with steam insulation jacketed pipes or additional insulation steam companion pipes to prevent medium crystallization.
– Rationale: This prevents blockages and ensures the valve operates smoothly.
Summary
By following these precautions and setting points, you can ensure that the safety valve is installed correctly and operates effectively, thereby maintaining the safety and reliability of the system. Regular inspections and maintenance are also essential to ensure the continued performance of the safety valve.
0